If you make a purchase using a shopping link on our site, we may earn a commission. Learn More
The Evolution of Multicolor Printing - the Bambu Lab A1 Combo Versus the Creality Hi Combo
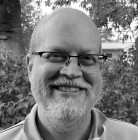
Bambu Lab A1
(~10.25 x 10.25 x 10.25 in)
Vs.
Creality Hi Combo
(~10.25 x 10.25 x 12 in)
Bambu Lab didn’t originate the idea of multifilament 3D printing, but they did set the standard with the AMS (Automatic Material System), introduced with their original X1C in September 2022. The AMS evolved into the AMS lite, included with the A1 mini Combo in September 2023, and the AMS lite was used again with the A1 Combo in December 2023.
The Bambu Lab A1 Combo consists of the A1 3D printer and the AMS lite. The A1 is a 500mm/s 3D printer with an all-metal direct extruder and quick-swap nozzles. All axes ride on linear rails. It has nozzle strain-based automatic bed leveling and Z offset. The AMS lite is an open four-filament feeder with filament detection and mechanical auto-retraction capability. An RFID reader reads tags embedded in Bambu Lab filament spools and sends color and type data to the printer.
In March 2025, veteran 3D printer manufacturer Creality caught up to Bambu Lab with a very similar proposition - the Creality Hi Combo, which consists of the Hi 3D printer and the CFS (Creality Filament System). The CFS is not entirely new; it was introduced with the K2 Plus Combo in July 2024. It is an enclosed, fully sealed four-filament feeder. It doubles as a filament dryer since it’s heated, with a fan distributing the heat and blowing air through desiccant, absorbing moisture. It’s equipped with a temperature and humidity display to show drying progress. Up to four CFS units can be connected to the Hi for up to 16 filaments, much like the AMS on the Bambu Lab X1 and P1 series.
The Bambu Lab A1 Combo obviously influenced the Creality Hi Combo. While Bambu Lab was the first to market with a printer and multifilament unit like the A1 Combo, Creality has had time to examine the competition, correct any shortcomings, and innovate to provide a compelling alternative.
Shared Features
The printers are so similar that it might appear that Creality cloned the Bambu Lab A1 Combo. This isn’t the case, but first, we’ll go through the similarities.
Speed
Both printers are rated for 500mm/s peak printing speed, the high-speed standard established by the Bambu Lab X1C and carried over to most subsequent Bambu Lab printers, including the A1. All manufacturers try to compete with this speed, so while this speed was once ground-breaking, it’s come to be expected at the time the Creality Hi was released.
Design
The Bambu Lab A1 is an open-frame 3D printer with a Z axis gantry on top, structural members shrouded in curved plastic throughout, giving the printer a sleek, finished look, and a full-color touchscreen on the right side.
The Creality Hi follows this design very closely.
Temperatures
The nozzle and print bed temperatures on both printers are identical. Both nozzles can be heated up to 300°C, making them easily capable of printing higher-temperature filaments like PETG and TPU. This also requires the extruder assemblies to be all metal since exposing Teflon to temperatures above 260°C causes dangerous fumes.
The beds of both printers are capable of being heated up to 100°C. This enables the printing of tricky filaments requiring careful bed adhesion techniques like ABS and ASA, though these are better printed in fully enclosed printers to retain heated air and prevent the release of toxic gas.
Extruder Type and Cable
Both printers use direct extruders. This is no surprise, as Bowden extruders have fallen out of favor lately, and no new Bowden extruder-equipped printers have been made in the last few years. Direct extruders and their motors have gotten light enough and the drive systems powerful enough that these extruders can be driven at high speed with good results as long as techniques like input shaping and vibration compensation reduce or eliminate the resulting ringing artifacts that might appear in the print.
Both extruders are connected to the rest of the printer with a single USB-C cable containing all the power and data wires tightly bound in a tough, flexible cable. This becomes a greater necessity at high speed.
Structure
Dual Z axis leadscrews used to be considered a premium feature, but have come to be expected in printers of this size. The A1 has this feature, and Creality does not want the Hi to be left behind its competition, so it also has dual Z axis leadscrews.
High speed printing will cause rapid wear to POM wheels used to move axes on older printers, so linear rails are used on all axes on both printers.
Control
Printing at 500mm/s will cause severe print defects unless measures are taken. Linear advance looks ahead a few lines in the G-code and slows down the print head before sudden direction changes, such as corners. Vibration compensation uses an accelerometer to detect vibrations in the printers’ moving structures, with the printer compensating for the vibrations.
Both printers make use of both of these techniques.
Cameras
The two printers use cameras with translucent privacy filters that flip sideways to cover the camera lens when desired. They look almost identical.
Connectivity
Wi-Fi connectivity has slowly become standard in 3D printers. Both of these printers connect to the network by Wi-Fi. This allows each printer to connect to their respective phone apps, which allow printing from an online model database, using slicing in the cloud.
Bed Leveling and Auto Z Offset
Both printers use strain-based automatic bed leveling and Z offset. The nozzle taps the bed in a grid pattern for leveling and also sets the Z offset. Since this determines the exact location of the bed, it is very accurate for both bed levelling and Z offset.
Differences
The printers themselves have many similarities, but they’re not identical, and there are vast differences in the multifilament feeder systems.
Multifilament Systems
The Bambu Lab A1 Combo uses Bambu Lab’s second-generation multifilament unit, the AMS lite (Automatic Material System lite). It is a four-filament fully open design, with two filament spools on each side. The spools are mounted on spindles that grip the spool from inside the hub. This means there’s good compatibility with different spool types - cardboard and plastic - and it can even accommodate damaged spool rims since the spools are gripped from inside the hub. RFID readers read data off RFID tags mounted in Bambu Lab filament spools and send material and color data to the printer.
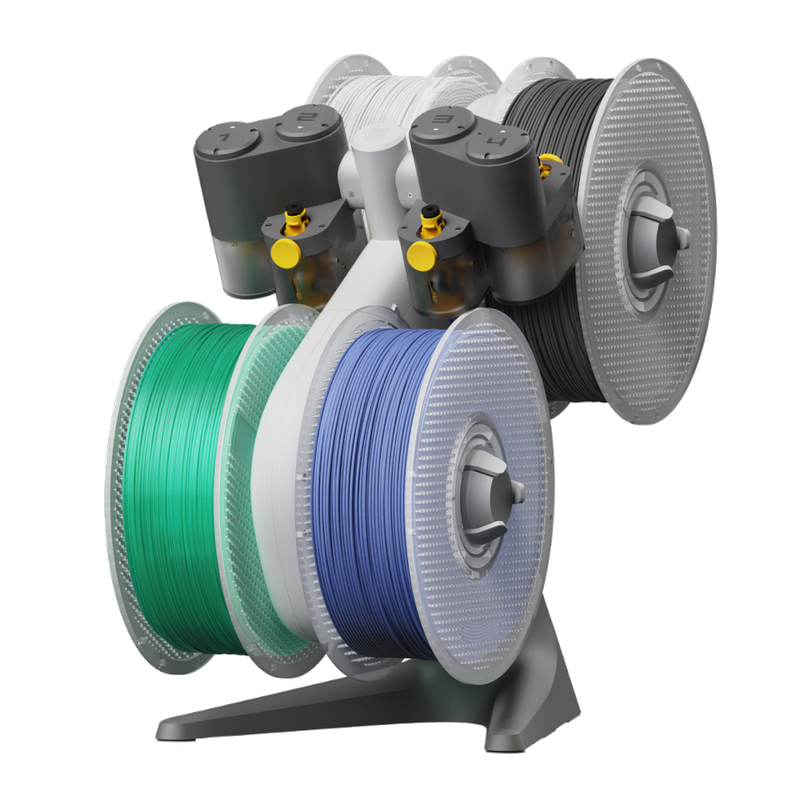
Creality’s CFS (Creality Filament System) is quite different. The only similarities are that it houses four filament spools and that it has RFID readers, though for Creality filament spools. But the CFS houses its four spools side by side in a sealed chamber. The CFS doubles as a filament dryer - it is heated and ventilated, and holds desiccant to absorb moisture. A digital readout on the front displays temperature and humidity. Up to four CFSes can be connected to the printer, meaning the printer can use up to 16 filaments, while only one AMS lite can be used with the Bambu Lab A1, allowing it to only use up to four filaments.

The differences in these multifilament feeders can also be seen in the printer’s extruder. The Bambu Lab A1 has four filament tubes from the AMS lite leading to a hub at the top of the extruder. But the Creality Hi’s CFS has only a single tube leading to the printer, with the switching occurring at the CFS, not the extruder. This simplifies the extruder connections, significantly reduces bulk, and leads to less mass being thrown around as the extruder moves back and forth.
The CFS arrangement is similar to Bambu Lab’s first-generation multifilament system, the AMS. It provides a stable environment for potentially sensitive filaments, and Creality’s addition of filament drying capabilities adds functionality. The drawback of such a system is that rollers support the rims of the filament spools - the spools are not held in any other way. This means the rims must be perfect. Many cardboard spools will not work, especially warped ones. Sometimes printed rim stiffeners can help.
It seems that Bambu Lab has been paying attention to the CFS and introduced the AMS 2 Pro and the AMS HT about 8 months after the CFS’s release. These are also sealed, heated filament feeders intended to dry filament. But only the AMS HT high temperature single filament feeder has a digital display, and it adds a remaining drying time reading. The A1 will be compatible with the AMS 2 Pro and AMS HT with a firmware update released in Q3 2025.
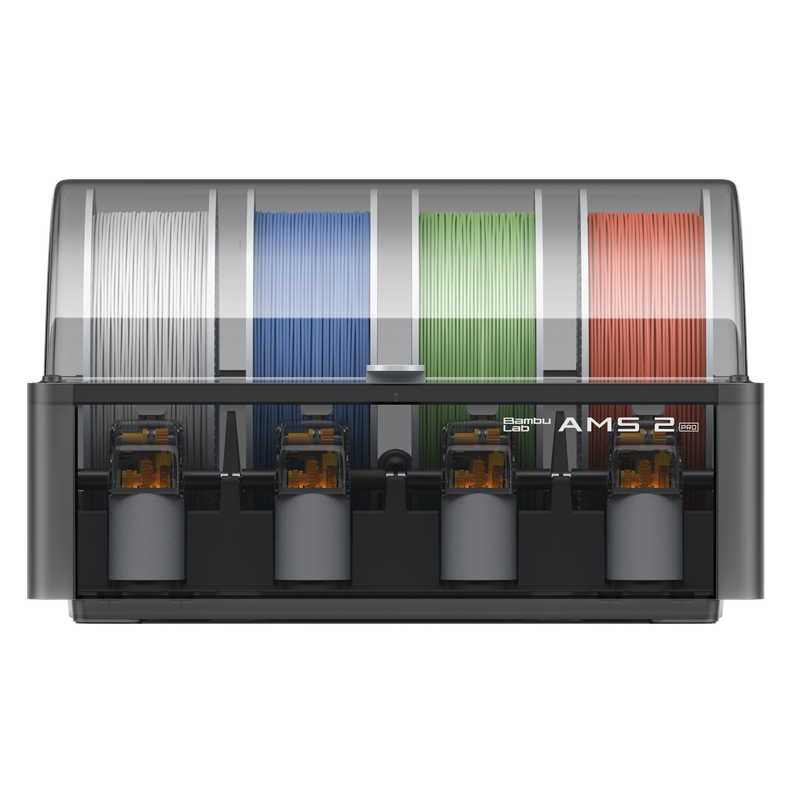
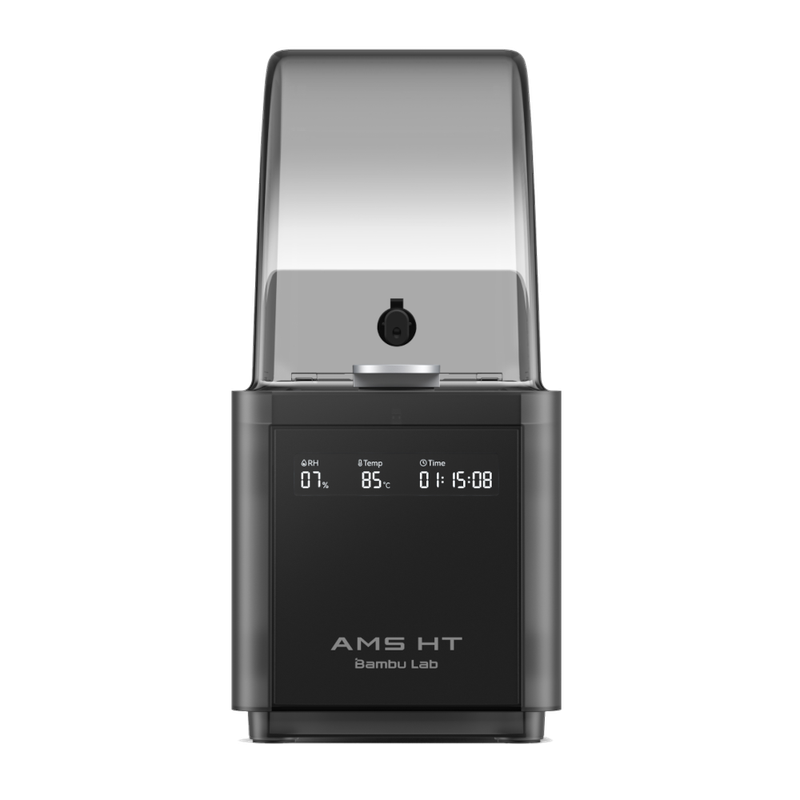
Print Volume
At first glance, the printers have remarkably similar print volumes. The X and Y dimensions are just about identical. The Bambu Lab A1 is 256 X 256mm while the Creality Hi is 260 X 260mm. The Creality Hi is larger, but only by 4mm. Most users won’t notice.
The critical difference is the Z dimension. The Bambu Lab A1 allows printing up to 256mm high objects, while the Creality Hi’s print height is 300mm. This is a significant difference and will definitely be enough to notice.
Touchscreens
The full-color touchscreens are similar but not identical. The Bambu Lab A1’s touchscreen is 3.5”. The Creality Hi’s touchscreen is 3.2”. A larger difference is that the Creality Hi’s touchscreen can be tilted for visibility and folded in to save space, while the Bambu Lab A1’s touchscreen is rigidly mounted.

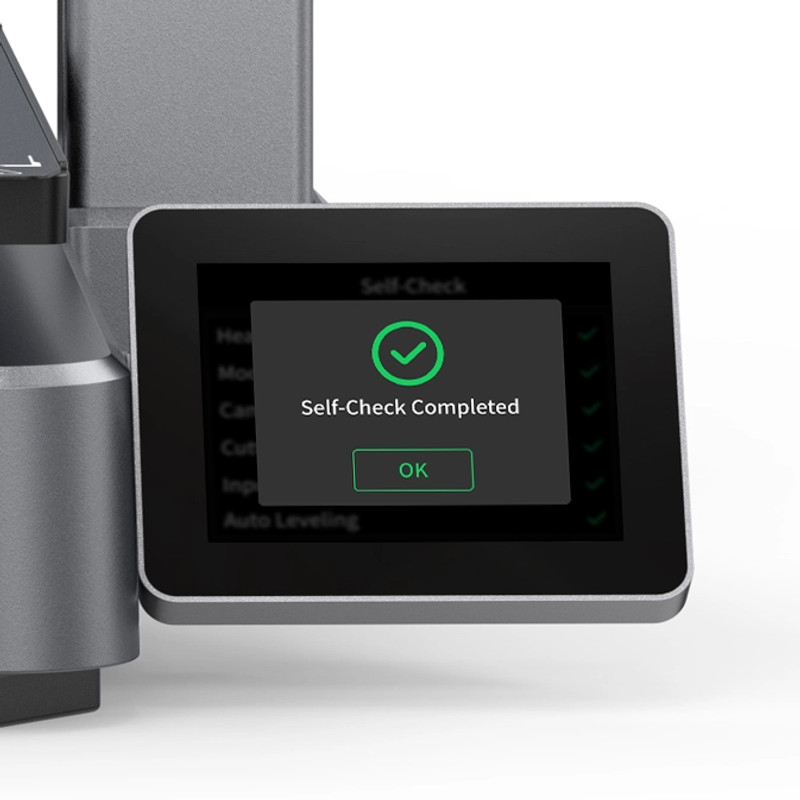
Print Bed Material
The Bambu Lab A1 is equipped with a double-sided textured PEI print surface on flexible spring steel that sits on a magnetic sheet. Smooth PEI print surfaces are optional, as are “SuperTack”, “3D Effect”, and many 3rd party varieties. Creality uses epoxy-coated spring steel instead of PEI on the Hi and several other printers. It was first introduced in the K2 Plus, and it has a good reputation.
Motors
Bambu Lab doesn’t disclose what type of motors are used in the A1, aside from the fact that they have silent drivers. They are conventional stepper motors, standard on every 3D printer made when the A1 was introduced. They accelerate the A1’s moving components at the rate of 10,000mm/s2. This was considered very fast for a Cartesian printer at the time of its release.
Creality specifically states that the X and Y axis motors on the Hi are “step-servo” type, with traditional stepper motors for the Z axis and extruder. Step-servo motors are a higher performance, more advanced, more expensive design and new to 3D printing. Creality drives the motors using FOC (field-oriented control) algorithms, which independently control the torque and magnetic flux of the motor. This allows the motors to move components with 12,000mm/s2 acceleration.
Heat Bed
The Bambu Lab A1 uses a conventional method to heat the bed, with 24V power from the DC power supply. The power supply’s capacity restricts the amount of power available for bed heating, since it also has to power the nozzle heater, all the motors, and the control electronics. The A1 has a 350W power supply for all these functions.
The Creality Hi heats the bed with an AC heater. This takes AC power right from the wall outlet, bypassing the DC power supply. Creality has rated the heater at 1000W. This makes for very fast heating of the large bed surface area. Such heaters heat the entire bed as quickly as the nozzle.
X Axis Tilt Reduction
The Bambu Lab A1 has dual Z axis leadscrews supporting the X axis crossbeam, but these are driven by a single motor and synced using a belt at the bottom. The belt should ensure that the leadscrews are synchronized and the X axis crossbeam remains level. If they ever get out of sync, the Z axis will have to be disassembled and the crossbeam manually leveled.
The Creality Hi uses dual motors to drive the two Z axis leadscrews. The motors are electronically synced and should remain in sync to within a step or so - typically 1.8 degrees of rotation. If they ever get out of sync, the X axis crossbeam can be leveled automatically without disassembly. This calibration routine is built into the Hi firmware.
Built-In RFID Reader
Both the Bambu Lab A1 and the Creality Hi can use a single filament spool without their multifilament feeders. On the Bambu Lab A1, the filament parameters of this spool must be set manually.
The Creality Hi is the first 3D printer with a built-in RFID reader. It will read the filament parameter data off any Creality spool placed on the right side of the printer. This is a bit of a compromise since the spool is mounted on the top of the printer, but without a top-mounted reader that can read the RFID tag on the side of the spool, it can still offer convenience.
Sounds
Both printers play sounds when the print finishes or is paused. This is a very unusual feature, used on only these two printers, plus the closely related Bambu Lab A1 mini, the A1’s predecessor.
However, each printer uses an entirely different method to produce sound. The A1 uses its motor controllers to vibrate the motors at the desired frequency, producing sound in an unusual way. The Creality Hi uses a much more conventional piezo buzzer.
Filament Cutter
Multifilament 3D printers have to use filament cutters when changing filaments to abruptly stop feeding one filament so they can switch over to another. This is accomplished using a filament cutter, a blade that pushes against the filament, cutting it.
On the A1, the X axis motor pushes the extruder beyond the edge of the bed line, onto a pin that pushes a lever attached to the filament cutter, cutting the filament. This requires a lot of force and puts strain on the motor and belt. The Creality Hi uses an electromagnet to move the blade. This greatly simplifies the mechanism and reduces the number of moving parts.

Filament Run-Out Sensor
While both printers have filament run-out sensors, the Creality Hi places it inside the extruder, as close as possible to the nozzle. This minimizes waste by shortening the length of filament that must be purged before new filament can be directed to the nozzle. The Bambu Lab A1’s filament run-out sensor is just below the filament hub. It’s much closer to the nozzle than many other printers, but not as close as the Creality Hi’s design.
Verdict
Bambu Lab has had success with their A1. They corrected problems with the heat bed cable early on, and the printer has proven economical, fast, accurate, and reliable ever since. The AMS lite has also developed a reputation for reliability.
But Creality had the opportunity to study the A1 for 15 months, an eternity in the fast-moving 3D printer world. They took their time to develop a response to the A1 and pioneered the technologies in earlier printers, using the CFS and the epoxy build plate introduced in the K2 Plus eight months earlier. They have developed technologies that were unavailable when the Bambu Lab A1 was introduced, like the step-servo motors, improved X axis leveling by using dual leadscrew motors, and revisited certain rare premium features like the AC bed heater.
Their CFS is well thought out and has the advantage of doubling as a filament dryer. There are no half measures with this functionality - the heat is distributed by a fan, the liberated moisture is absorbed by desiccant, and both the temperature and humidity are monitored. Though the filament selector in the CFS complicates the mechanism, it leads to a simpler, lighter, single tube connection to the extruder. And there is the possibility of up to four CFSes connected to the Hi for a total of 16 filaments, something Bambu Lab can’t offer with the A1 Combo.
Pricing should also be taken into account. The A1 is older, with a much less sophisticated and far less expandable multifilament feeder system. To match the filament drying feature of the Creality Hi Combo, you would also need to add a high-end four-spool filament dryer to the A1 Combo. So the Bambu Lab A1 Combo might be a worthwhile alternative to the Creality Hi Combo if it was available at a discount. But this is currently not the case - in fact, the Bambu Lab A1 Combo is far more expensive than the Creality Hi Combo.
Given this pricing discrepancy and all the improvements Creality has made to the high-speed open-frame printer plus multifilament feeder system, we would recommend the Creality Hi Combo.
Click here to view the Bambu Lab A1 on the Bambu Lab website.
Click here to view the Creality Hi Combo.
You can find a side-by-side comparison of the specifications for these two printers in the table below: