If you make a purchase using a shopping link on our site, we may earn a commission. Learn More
Comparing the Bambu Lab X1 Carbon Combo vs the Prusa MK4
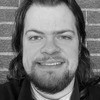
Bambu Lab X1 Carbon Combo
(~10.25 x 10.25 x 10.25 in)
Vs.
Prusa MK4
(~10 x 8.25 x 8.75 in)
In this article we will take a closer look at the differences and similarities between the Bambu Lab X1 Carbon and the Prusa MK4.


Bambu Lab came to be after a successful Kickstarter campaign in 2022. Using the funds raised, they sought to develop and deliver professional and feature-rich 3D printing in a package that is both easy to use and accessible. The X1 Carbon, or X1C, is Bambu’s flagship printer and was the first product launched following their initial funding. Sales of the X1C began in May of 2022, and the X1C Combo, an upgraded version of the X1C capable of automatically switching between multiple filaments, followed later in the year.
Prusa is an older name in the 3D printing world, getting a start in 2012. Since then, the manufacturer has iterated several times on their i3 design. In March 2023 their own flagship, the MK4, debuted as the latest iteration of this platform. The upgrades were long awaited by the community surrounding Prusa, as the prior MK3 model had been on sale for around 5 years by the time the MK4 was released.
The MK4 launched around half a year later than the X1C Combo, making the two top level printer offerings natural competitors. The two models are quite similar in their basic capabilities, but they also have some huge differences in the features that are offered by each. We’ll start by summarizing the similar ways in which these two premium machines operate.
Similarities between the Bambu Lab X1 Carbon Combo and Prusa MK4
Extruder and hot-end
Both of these printers utilize a direct drive extruder with an all metal hot-end. In this configuration, they have extruders that are compatible with most standard filament materials. The maximum hot-end temperatures of the MK4 and the X1C are 290 ℃ and 300 ℃ respectively. Effectively, these temperatures are both sufficient for printing with most materials, including those that have a higher melting point like ABS.
Each extruder directly drives filament extrusion with a motor and gearbox. The Bambu X1C and Prusa MK4 have a design that is conscious of keeping mass concentrated as close to the toolhead movement axes as possible; the use of gearboxes enables coupling to a pancake-style motor that has less mass in a smaller package than a traditional drive motor. They also utilize a couple sensors that provide peace of mind, including a hall sensor to detect if filament runs out during a print and thermistors for accurate temperature control. While the base performance of these two extruders will be near identical, the X1C extruder includes a few additional useful features that we will discuss later in the article.

Print Speed
Both of these flagships adeptly exhibit one of the most sought after 3D printing performance metrics: speed. They achieve high printing speeds by using specially developed software and calibration. At a hardware level, the MK4 is theoretically capable of a max toolhead speed of 600 mm/s, while the X1C can achieve 500 mm/s. While it may seem the MK4 would be a bit faster due to this, the real capability in printing speed lies in the software of the printer.
When printers move quickly, the rapid acceleration of mass can induce vibrations or resonances in the system. This can translate into imperfections in the print as these vibrations knock the extruder slightly off course while it follows the gcode pathing. Prusa and Bambu have implemented a process known as Input Shaping to prevent this. Input Shaping is a special algorithm and printer calibration that can predict these vibrations and automatically correct for them while printing, allowing the printer to work at much higher speeds while still achieving the same print quality.

Another way that the software of these printers enables higher speeds is the use of another process called Pressure Advance. This refers to a calibration that can better predict the needed flow rates of filament in various parts of the prints. For example, when moving quickly on a long, straight portion of the print, the extruder will have to rapidly deposit material to account for the speed. Conversely, if a part has many corners, the extruder will be moving more slowly and will need to extrude less material in order to avoid material blobbing at the edges of the print. Both the X1C and MK4 use these processes to achieve similar high printing speeds without compromising the quality of the print.
Automatic Bed Leveling
Both the X1C Combo and MK4 offer automatic bed leveling as a feature. This refers to the process a printer completes at the beginning of a print to ensure the printing surface is flat relative to the print layer. The MK4 achieves this using a load cell sensor on the toolhead that touches off at the bed in the print area, while the X1C used load cells located in the bed assembly itself for the same exercise. The X1C’s leveling method achieves a high level of accuracy since the printing nozzle itself actually touches off to the bed for each reading. Utilizing sensors that are not directly touching the printing nozzle does leave some margin for error if the sensor is out of its expected position. The printers calculate a mesh that represents the print bed and can automatically account for any small differences in Z-height that may exist in the printing surface itself. This also allows them to print the first layer at an ideal height, which is extremely important to ensure that the print adheres to the build plate properly. This premium feature is a huge plus for both of these printers, as manual bed leveling can take some time and be tedious and inconsistent.

Connectivity and Monitoring
Both Bambu and Prusa offer connectivity options that allow you to remotely monitor, control, and push printing jobs to the printers. Each manufacturer has their own software that works well with their respective printers.
The X1C is capable of a Wi-Fi connection out of the box and integrates closely with the Bambu Studio software. This program includes both a slicer to create gcode from 3D models as well as control and monitoring UI for the printer itself. It supports the ability to monitor camera feeds from the printer as well, which allows you to check in and see how a print is going from anywhere at any time.
The MK4 also has Wi-Fi capabilities built in. Prusa’s connectivity software, called Prusa Connect, does not itself include a slicer but otherwise has very similar capabilities to Bambu Studio. The lack of slicer however is not an issue, as the ever popular Prusa Slicer software is also available for use, and works seamlessly with Prusa Connect. It even offers the ability to monitor camera feeds, though unlike the X1C the MK4 does not come factory-equipped with a camera; we will explain the details of that in a later section.
Differences Between the Bambu Lab X1 Carbon Combo and the Prusa MK4
The MK4 and Bambu X1 Carbon may be similar in their use of modern printer design and algorithms for timely printing, but they also have some clear differences in capability. Here we will discuss these differences to help you decide which printer is better for your own use case.
Construction and Enclosure
The two printers each have a significantly different geometry used in their construction. The MK4 uses a large rectangular cast aluminum frame with two vertical posts to support axis mounts and provide rigidity and support during printing. The X1C on the other hand has a cubic, welded steel frame that fully encloses the print area with 4 vertical members, one at each corner. It does not appear that one construction is particularly advantageous over the other from the perspective of print performance - however the X1C construction and material does result in a heavier printer that likely induces fewer vibrations while active.
Another striking difference between the two is the use of a printing enclosure. The MK4 has a completely unenclosed build space that offers less control over items such as ambient temperature - this can make it more difficult to print higher temperature materials such as ABS. These materials do not perform as well in printing without an enclosure as they can cool at inconsistent rates without controlled air temperature and fan drafts. This inconsistent cooling results in shrinkage that can warp and delaminate layers within the print. With the X1C, this is not a worry; panels are affixed to the frame to completely enclose the print area. The X1C enclosure also helps to control fumes and even includes a carbon filter to ensure that the air leaving the enclosure is clean. An enclosure can be purchased separately for the MK4, but it cannot be ordered equipped with an one out of the box.

Motion System
The printers also use different motion systems. The X1 Carbon uses a system called CoreXY, where the extruder itself is able to move in both the X and Y directions, while the Z axis is controlled by build plate movement up and down. The MK4 on the other hand utilizes a more traditional Standard Cartesian or bedslinger design, where the extruder moves only along the X axis in any given layer, and shifts up in Z when the layer is complete. The Y direction is handled by motors that move the entire print bed along the axis. Typically it would be assumed that CoreXY could allow for faster printing due to the lower amount of mass moving on the higher speed axes (X and Y), but the MK4 and X1C in practice print at similar speeds, likely due to each having built in compensation for vibrations and resonance.
Build Volume and Physical Size
Each machine features a different printable volume and physical size, listed below:
- Bambu X1C Combo - Max. Build Volume: 256 × 256 × 256 mm, Printer Size: 389 × 389 × 458 mm (AMS system can be placed independently of the printer and is not included in Printer Size)
- Prusa MK4 - Max. Build Volume: 250 x 210 x 220 mm, Printer Size: 500 x 550 x 400 mm
The bedslinger design of the MK4 results in a much larger physical footprint for the printer, despite not having an enclosure and achieving less printable space than the X1C. The X1C does take up a little more vertical space, but this allows for about 36 mm of printable space in the Z direction. The X1C Combo specifically includes the AMS system (discussed later in the article) which can be placed anywhere nearby and takes up additional table space or sits on top of the printer. Wherever it is set up, the AMS physically occupies 368 × 283 × 224 mm. If you are limited on space or need to print larger objects, you may want to consider the space and print area advantage of the X1C over the MK4.
Extruder and hot-end
Though the extruder design at a base level is very similar between the MK4 and the X1C, they each have some small features and advantages exclusive to their design. To start, each printer uses a different material tube to feed filament into the hot-end. The MK4 utilizes a durable, all metal design; this style can be prone to clogging as the metal conducts heat and filament melts before the nozzle, but the MK4 uses effective heat sinking and cooling to prevent this. The X1C alternatively uses a PTFE tube, which does not conduct heat but over time could be damaged by high temperatures and abrasion, requiring replacement. Additionally, the MK4 nozzle and extrusion tube are designed as a removable unit with an adapter to allow quick and easy nozzle swapping, allowing more flexibility in choosing nozzle material and diameter. It is possible to swap the nozzle on the X1C as well, but it is not necessarily quite as simple as the MK4 design.

The Bambu X1C was additionally designed to handle nearly any filament material, including harsh filaments such as composite filaments with glass or carbon fibers in them. Out of the box, the printer is equipped with a nozzle and drive gears made from hardened steel. This allows for the use of these harsher, more abrasive filaments without the fear of wearing out the drive gears or nozzle with use. The MK4, on the other hand, comes equipped by default with a brass nozzle and mild steel gears. The brass nozzle will conduct heat better and heat more quickly, but is too soft to reliably handle the composite filaments mentioned above. Even so, the MK4 may be capable of printing some of these filaments if the nozzle is swapped to a hardened steel variant.

Lidar and Camera
A distinctive feature of the Bambu X1 Carbon printer from the MK4 is the use of a lidar sensor for leveling, in addition to the load cells on the print head. This adds a level of redundancy to the automatic bed leveling, and additionally allows the printer to check leveling even when the extruder is not in contact with the print bed. Both printers should be able to reliably complete automatic leveling, but the X1C has an extra level of redundancy that could help increase the reliability of this process in some situations.
The X1C also comes equipped with an internally mounted camera that monitors the print bed for certain failures and can stop or pause printing - the MK4 does not have any camera equipped as purchased. The X1C’s camera is capable of a 1080p picture and 30 frame per second video capture. The printer’s software uses image processing to execute checks on the first layer to ensure the automatic leveling was successful. It also continuously checks the print to determine whether or not a spaghetti failure is occurring. This is a wonderful feature, as a runaway spaghetti failure can create a large mess and can even damage the printer if it continues for long enough.

Print Bed
The printers have some slight differences in their print bed. Each uses spring steel plates for ease of removal from the magnetic heated bed, but the finish of these plates varies. The MK4 always ships with a smooth PEI plate, a desirable finish for adhesion and ease of print removal. The X1C heated bed can get slightly hotter than the MK4 (120 ℃ vs. 100 ℃) and ships with a randomly selected plate from two offerings: a textured PEI plate or Bambu Cool Plate (a double sided plate with smooth PC on one side and a hard thermoset for engineering materials on the other). Both plates are compatible with the lidar sensor, and each have their own advantages and disadvantages for printing with specific materials. Additional build plates can be purchased from either manufacturer, with finishes suitable for printing most filaments. The smooth PEI plate is probably the best option for general purpose printing, while the Bambu Cool Plate is a good hybrid option for printing with some harsher materials as well on the thermoset side.
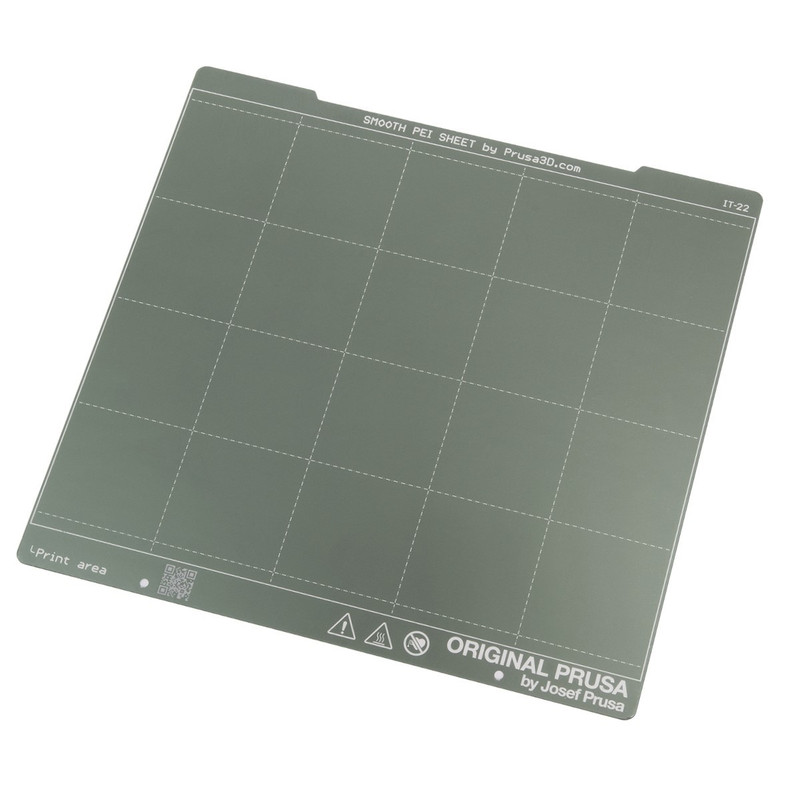
Multi Material Printing Compatibility
A defining feature of the Bambu Lab X1 Carbon Combo is that it includes the Bambu AMS, or Automatic Material System. If you have purchased the X1C on its own, you can still purchase the AMS separately, but the combo package includes these features out of the box. The AMS is able to hold 4 spools of filament and actively switch between them either during a print or between jobs. It will automatically cut the filament, select and load the next material, and purge the old material in the extruder into a waste chute. Additionally, the AMS is an enclosed environment that can protect filaments from contaminants and moisture in the air that may degrade them over time.

The MK4 does not have this capability, and filaments must be switched manually in between print jobs. Prusa does offer a multi-material upgrade, the MMU3, that can be purchased separately; it is not included in any printer packages and must be assembled and installed by the purchaser. We will discuss the MMU3 in more detail in the upgrades section.
Print Quality
While both printers are capable of an extremely high level of quality, the MK4 has a minor advantage due to the motors it uses. The MK4 stepper motors that control the X and Y axes have a tighter step angle of 0.9 degrees, while the motors on the X1C have a 1.8 degree stepping angle. The use of the precision motors reduces a phenomenon called Vertical Fine Artifacts, which are subtle vertical lines that can appear on a print, giving a slight, screen-door-like texture to the print. This phenomenon is extremely small and difficult to notice with the 1.8 degree step angle motors, but if you are trying to get the smoothest print possible without post-processing, precision motors may be an important feature for you.
Display and Controls
The display and user interface for each of these machines is another area of great difference. The MK4 utilizes a somewhat dated setup in this price range; the 3.5-inch color LCD display is useful for showing images of models and printer information, but is unfortunately not touch capable. The menus and controls must be navigated using a clickable scroll dial, which can be tedious, despite Prusa’s efforts to keep the UI simple. A plus for the MK4 is the fact that the printer has a convenient USB connector that allows you to use a flash drive to manually load gcode files to a printer when it is not connected to a network. If you prefer to use an SD card, the presence of a USB port offers the flexibility to use a dongle adapter for SD cards.
The X1C on the other hand has a larger 5-inch integrated color LCD touch screen that can be used to control and monitor the printer functions. These controls are compatible with the AMS system as well and can be used to adjust multiple material parameters. For loading gcode offline the X1C simply has a micro-SD slot, which should be enough for the majority of users.


The MK4 has a couple major upgrades available for purchase, while the X1C only has one. However, the X1C already has all the capabilities offered by the official Prusa upgrades, so it is not necessarily an advantage for the MK4.
The MK4 can be upgraded with an enclosure kit from Prusa that is conveniently configurable. Options are available for a lock, lighting LEDs, upgraded filtration systems, and even a fire suppression system (available to be sold and shipped by Prusa in the EU only). Additionally, it can be upgraded to multi-material capability with Prusa’s MMU3, allowing for automated switching and use of 5 different filament spools in printing. This upgrade does not have a shroud to protect filament like the Bambu system, but does offer one additional slot for filament over the AMS.

The X1C however, can overcome this if needed - additional AMS upgrades can be purchased on top of the one included with the printer. The software and firmware is capable of supporting 3 additional AMS modules with the separately sold AMS hub. This means that the X1C can be upgraded to support 16 filament multi-material printing, which is an incredible capability that most printers do not offer.
Both manufacturers do offer a wide array of replacement parts sold separately and offer instructions for some common repairs on their respective knowledge bases. Prusa, however, has a slight leg up in this department, as many components on the printer are 3D-printed and the models are made publicly available for repairs or upgrades. Additionally, their software and design is open source, inviting tinkers to contribute and modify to suit their own needs. This results in many unofficial upgrades for the MK4 being available on the web, which is a contrast to the closed source X1C design/software.
Assembly
As far as ease of assembly goes, the X1C Combo is a clear winner. The printer ships in a state that is nearly ready to go out of the box; the AMS requires some minor setup after unpacking, but other than that the printer is very plug and play. The MK4 is available to be purchased fully assembled, but customers will pay a premium of around $300 for this. The more economical option from Prusa requires the purchaser to fully assemble the printer themselves, which can take around 8 hours on average. This model is intentional, as Prusa caters to enthusiasts that would enjoy assembling the printer themselves and learning about each component. This may appeal to you if you are looking for a project or like to work with your hands, however, if you do not have the time or desire to put together your 3D printer, the X1C would be the better option.
Community and Resources
Prusa has a standing reputation of being very involved in their customer community. The company maintains forums for users to discuss and share upgrades, insights, and troubleshooting. Prusa also is extremely transparent and publicizes their code and many of the 3D models for parts of the printer. The MK4 is a favorite for enthusiasts and hobbyists due to these resources made available by Prusa.
Bambu is newer to the market and does not quite have the community or transparency that Prusa does. They do, however, have a rapidly growing user base that participates on their own forums and threads. Bambu is less involved in these discussions than Prusa, but they are not completely lacking in this regard and do offer quite a bit of useful information to users through these avenues.
Pricing
Both of these flagship consumer printers come at higher costs due to their richness in features and capability. The X1C Combo comes in at about $1550 at the time of writing, while the MK4 fully assembled is around $1100. The X1C does include features that are considered upgrades on the MK4; the enclosure and multi-material upgrade from Prusa would add nearly $650 to the price. Another pricing consideration is the fact that currently Prusa is only able to ship from the Czech Republic, which can result in hefty shipping prices depending on where you are located. Bambu, on the other hand, is able to ship from either China or a hub in the USA, which offers more flexibility in shipping. If you consider a higher shipping cost and purchase the enclosure and multi-material upgrades combined with the non-assembled MK4 kit, it would end up around the same price as the X1C Combo.
Should You Choose the X1 Carbon Combo or the Prusa MK4?
Both the X1 Carbon Combo and the MK4 are capable, top of the line printers. They each have a high level of performance in print quality, connectivity options, and printing speed. At a basic level, the experience you will have completing every day prints with each printer will be similar.
The X1C Combo has more features than the MK4 does out of the box, and could be a better choice if you need specific printing capabilities. The integrated enclosure is useful for printing higher temperature filaments, and the hardened steel nozzle and drive gears make the printer a great choice if you want to print with abrasive composite filaments such as carbon fiber. The MK4 is also technically capable of this, however, to do it effectively and reliably you may have to add a hardened steel nozzle. Additionally, the X1C Combo is capable of printing with multiple materials without the need to purchase additional upgrades. As an overall package, setup is easy and quick, making the X1C Combo a great choice if you are looking for a feature rich platform that does not involve any tinkering or fine tuning.
The MK4 on the other hand includes fewer features as purchased, but comes at a lower price and can be upgraded to similar capabilities. Even if the upgrades are purchased, the MK4 is slightly inferior when it comes to the screen and UI. Additionally, the MK4 lacks some convenience features that the X1C has, such as the camera, spaghetti failure detection, and backup lidar sensor for leveling. Assembly of the kit will be required to keep the price competitive, so the MK4 is only a good choice for you if you would like to take some time building and setting up the printer. If you are indeed interested in being hands on with the machine, the MK4 is a great choice with the information and discussion available in the Prusa community.
Click here to view the Bambu Lab X1 Carbon Combo on Matterhackers.
Click here to view the Prusa MK4 on Prusa3d.com.
You can find a side-by-side comparison of the specifications for these two printers in the table below: