3D Printer Extruder Guide
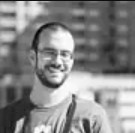
The extruder of a 3D printer plays a crucial role in pushing the plastic filament into the hot end, where it melts and is deposited onto the print bed. Ensuring that the extruder applies a consistent force to move the filament is critical since inadequate or excessive flow can lead to poor quality prints or even a total print failure.
As a result, it is vital that your 3D printer is equipped with a high-quality extruder and that you understand the potential problems that may stem from extruder issues. Before diving into the specifics, let’s familiarize ourselves with some fundamental terminology related to 3D printer extruders.
An Overview of Extruders
Various extruder designs exist, but they all share a few essential features:
- Typically, a spring applies pressure to push a motorized toothed pulley against the filament to grip and move it into the hot end.
- A stepper motor powers the extruder, similar to the ones responsible for moving the print head in the X, Y, and Z directions. E is often used as shorthand for the extruder’s stepper motor.
There are two distict extruder types you will see: Direct Drive and Bowden. While both have their pros and cons, we have found that direct drive offers a slight advantage and is our preferred choice. We will discuss the benefits of each in more detail below.
Bowden Extruders

Bowden extruders are positioned separately from the print head, usually on the printer’s side, and use PTFE tubing (also known as the Bowden tube) to guide filament to the hot end.
Advantages:
- The print head is lighter due to the separate extruder, resulting in faster printing and a reduced likelihood of artifacts like “salmon skin” caused by the added weight’s inertia.
- Upgrades and maintenance are easier, as the hot end and extruder can be modified independently and employ simpler designs.
- The simpler design typically means they are less expensive, leading to a lower overall printer cost.
Direct Drive Extruders
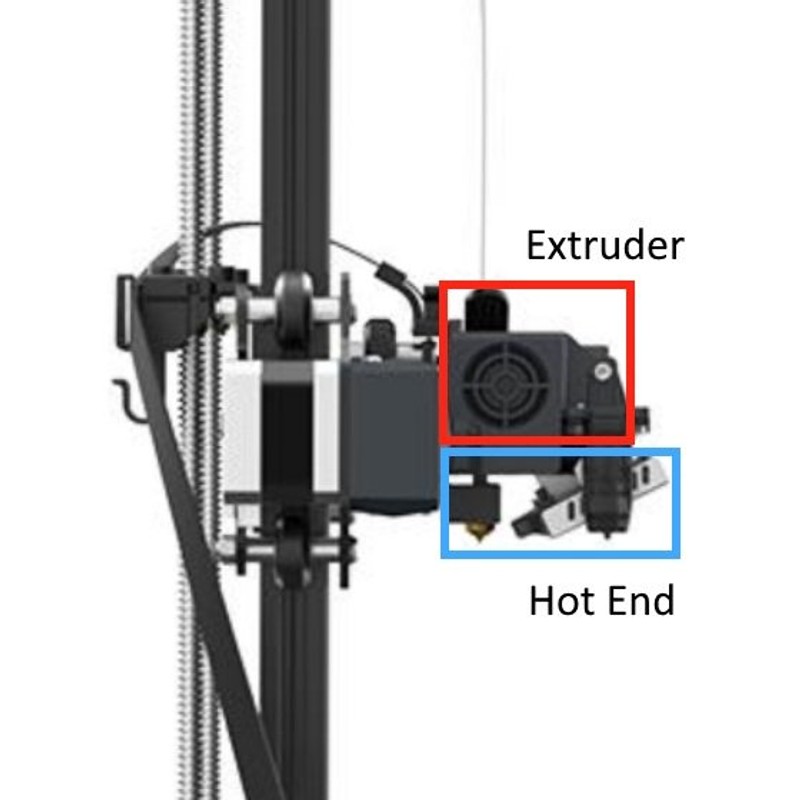
Direct drive extruders are mounted directly above the hot end, pushing the filament right into it. The extruder moves with the print head.
Advantages:
- The close proximity of the extruder and hot end allows for shorter retraction distances, making it easier to manage stringing and other print artifacts resulting from retraction.
- Less likely to jam, as the shorter retraction distance prevents hot filament from being pulled too far back into the hot end’s cool zone.
- Loading and unloading filament is easier.
- Printing flexible filaments like TPU is much simpler.
In our experience, direct drive extruders perform better overall than Bowden extruders, and we have found that they tend to be more reliable and consistant. Direct drive extruders typically come at a premium, but we feel it is usually worth the cost in the long run if you have the budget.
Extruder Gearing
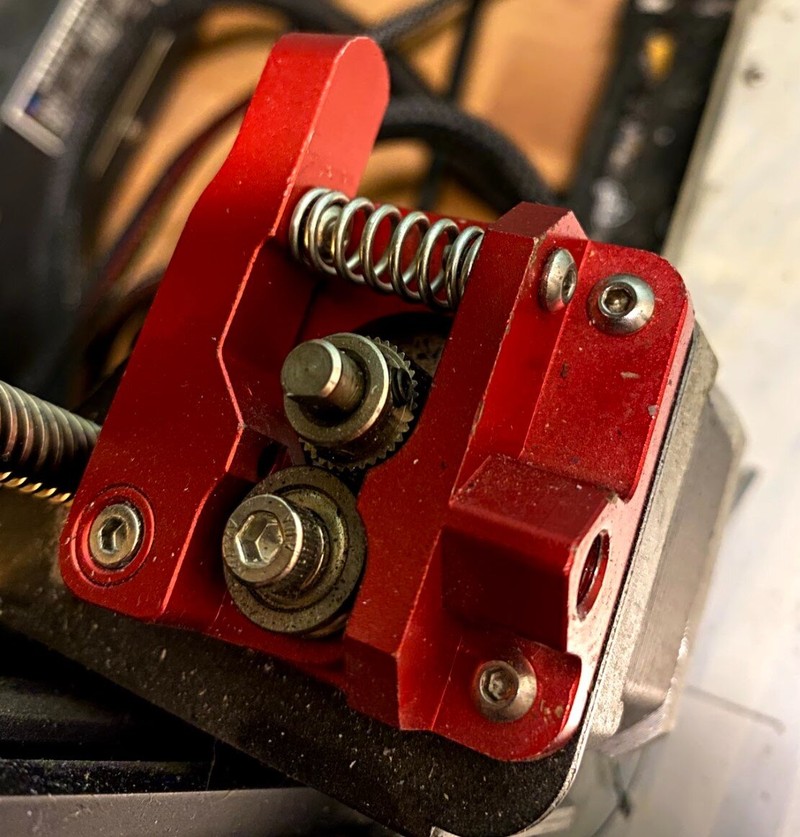
Extruder construction also varies in terms of the gearing between the extruder motor and the extruder gear that comes into contact with the filament. Bowden extruders typically mount the extruder gear directly to the motor, whereas direct drive extruders use extra gearing to fit within the tighter space above the hot end. Though additional gearing adds complexity, it does offer benefits such as increased torque from the extruder motor and finer control over filament movement.
That being said, we have had success with both geared and ungeared extruders, so we have not noticed a significant difference between the two. It is crucial to understand the distinctions when changing extruders, as you will need to adjust your printer’s E-steps setting, which determines how much the extruder should turn when pushing the filament a specific distance.