3D Printer Hotend Guide
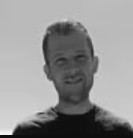
The hotend is the component that melts your filament, allowing it to be deposited layer by layer, forming a 3D printed object. Although it sounds straightforward, maintaining a specific temperature is key for quality printing. Another vital role of the hotend is ensuring the filament only melts at the nozzle, remaining cool and solid beforehand.
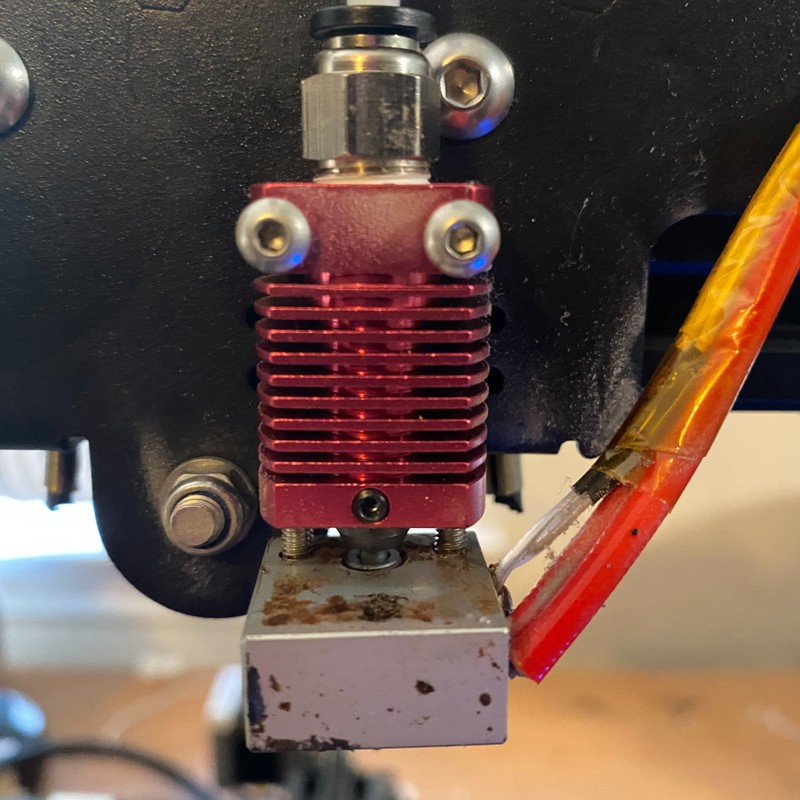
Hotend designs vary between printer models and manufacturers, but they all use the same basic method of heating filament. Following the filament’s path, you’ll notice that it initially passes through the extruder, which is either on the side of the printer in a Bowden setup or directly above the hotend in a direct drive setup, and is responsible for propelling the filament towards the hotend. Subsequently, the filament travels to the hotend and is ultimately deposited onto the print bed to form the printed piece.
How the Hot End is Heated
The thermistor and heat cartridge collaborate to maintain the correct temperature.
You will see two sets of wires exiting the heat block’s side. These wires connect to the Thermistor and the Heater Cartridge, which work together to keep the hotend at the desired temperature:
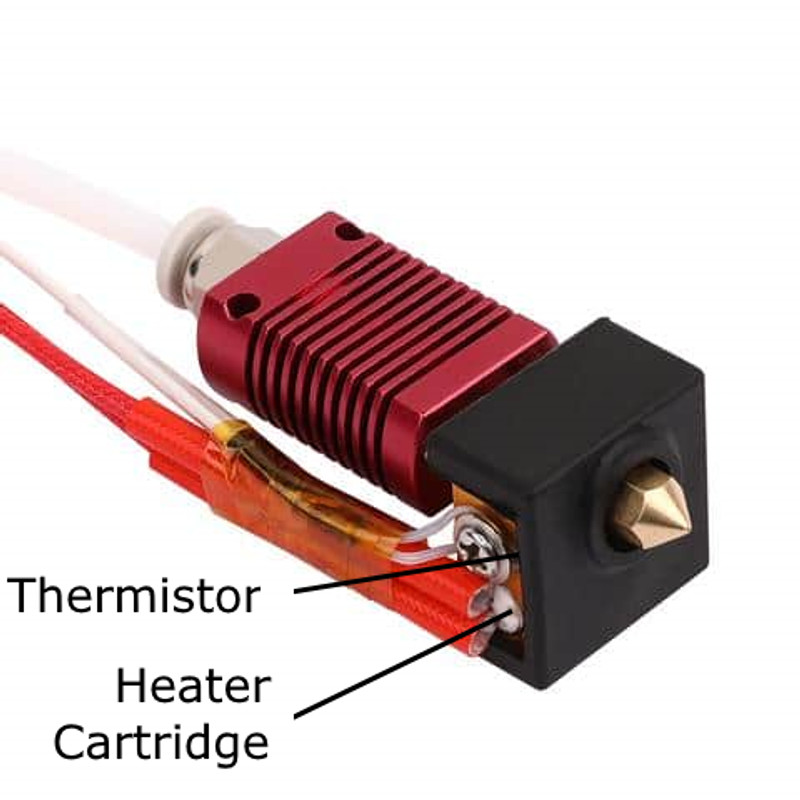
- The Heater Cartridge generates heat when powered by the printer. This heat spreads through the heater block and the nozzle, and eventually to the filament. The larger red wires connect this component to the printer’s mainboard.
- The Thermistor measures the temperature, which the printer controller uses to turn off the heater cartridge once the temperature surpasses the set point. The smaller white wires connect the thermistor to the printer’s mainboard.
Together, these parts ensure that the hotend stays at the desired temperature, typically from 200C to 260C depending on the material you are using.
The Hot and Cool Zones
The hotend features two distinct temperature zones: the lower hot zone, heated by a heater cartridge, and the upper cool zone, cooled by a heat sink and fan.
As the filament enters the hotend through the PTFE tube, it remains cool and firm while passing through the cool zone. As the filament moves into the hot Heat Block and Nozzle, it quickly heats up to its melting point before being deposited onto the print.
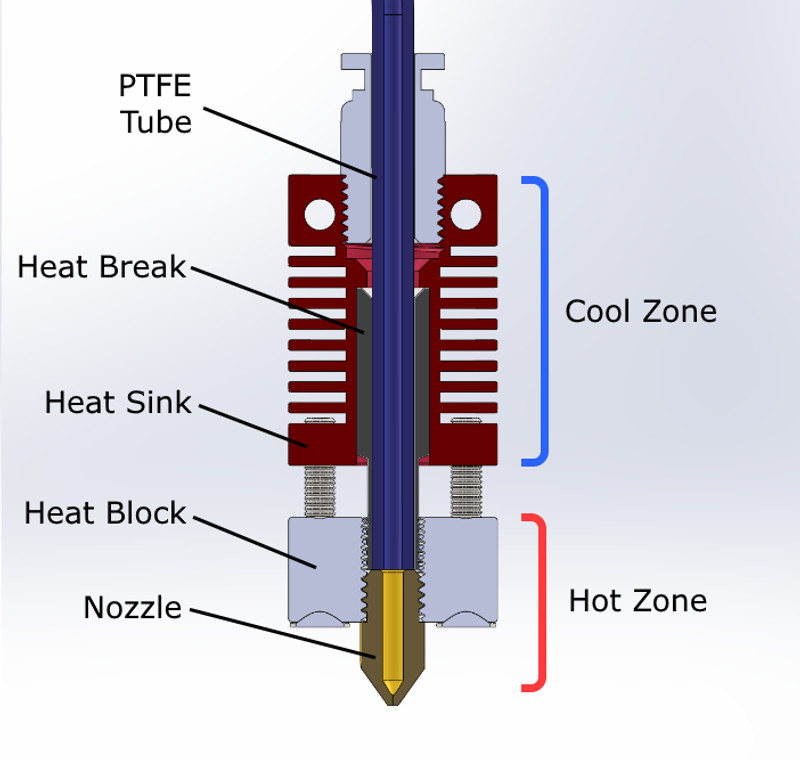
Note the Heat Break surrounding the PTFE tube, spanning both zones. It is thin in the empty space between the hot and cool zones, minimizing heat transfer to the cool zone. However, some heat still escapes to the cool zone, necessitating a Heat Sink and Hot End Fan (not pictured) to maintain its cool temperature.
You might wonder: Why is it essential to keep the filament cool until it reaches the nozzle? The reason is to prevent filament jams in the hotend. If the filament melts or softens prematurely, the pressure from pushing the filament will cause it to widen, which is undesirable. The friction from the expanded filament against the PTFE tube’s walls results in filament jams in the hotend, leading to print failures.
Standard vs All-metal Hotends
Standard hotends typically utilize a PTFE liner within the heat-break and the throat, which reduces friction between the filament and the hotend’s interior surface. This design is advantageous when printing with low-temperature materials like PLA and TPU, as the PTFE liner helps to minimize clogging and facilitates smoother extrusion. However, the presence of PTFE limits the maximum operating temperature of standard hotends, making them unsuitable for printing with high-temperature materials. Additionally, PTFE liners can degrade over time, affecting print quality and requiring eventual replacement.
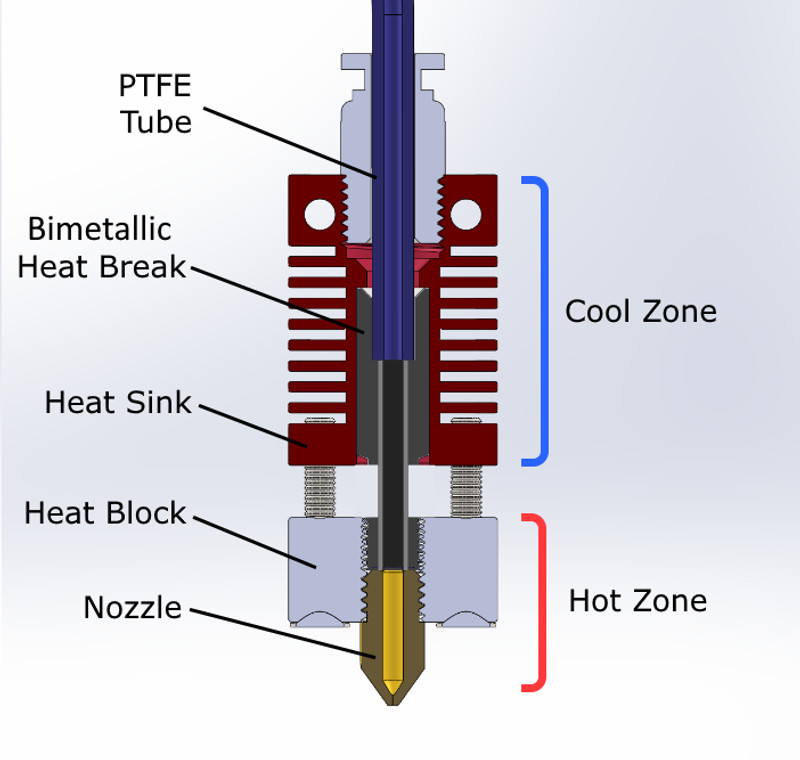
Some 3D printers utilize a more premium an all-metal hotend, which are made entirely of metal components, typically stainless steel or aluminum. The absence of plastic or PTFE parts in the heat-break or the throat allows all-metal hotends to withstand higher temperatures. This makes them suitable for printing with a wider range of filaments, including high-temperature materials like Nylon, Polycarbonate, and certain blends of PETG. Additionally, PTFE is prone to wearing over time when exposed to high temperatures, and will eventually cause frequent jamming until it is replaced.
All-metal hotends are known for their excellent heat dissipation, ensuring consistent and accurate extrusion. However, they may be more prone to clogging due to the lack of a PTFE liner, which can make printing with certain low-temperature materials like PLA more challenging. In recent years, many all metal hotends use a bimetallic heat break, which we have found does a better job at keeping the heat on the hot side than older all-metal hotend designs, and largely address this issue.
Conclusion
Understanding the basic function and inner workings of a hotend is crucial for successful 3D printing. You’ve learned that hotend’s primary purpose is to melt the filament, allowing it to be deposited layer by layer to create a 3D printed object. To ensure quality printing, it is essential to maintain a specific temperature and keep the filament cool until it reaches the nozzle.
With variations in hotend designs across different printer models and manufacturers, the same fundamental heating principles apply. By comprehending the roles of the thermistor, heater cartridge, and hot and cool zones, you can better troubleshoot potential issues and optimize your 3D printing experience.